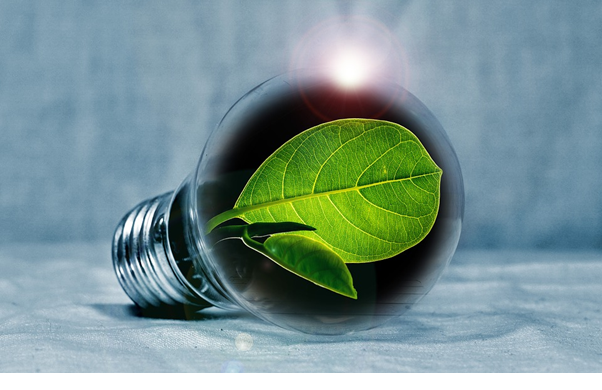
In line with the company’s Environmental Standard ISO14001, Plater Group is committed to reducing the company’s impact on the environment as a sustainable business. To that end, we have decided to embark on two energy saving initiatives that will significantly reduce our energy usage allowing the company to reduce its impact on the environment.
New Compressor
The company is purchasing two new compressor units to provide the necessary compressed air to run the Glossop site.
Compressed air is used in a variety of processes and is fed via a compressed air ring main. The existing compressor is a unit manufactured in 1992 and has served the company well up to now.
Technology regarding compressing air has come on ‘leaps and bounds’ since 1992 and today’s modern compressors are much more energy efficient. The two new compressor units will use much less electricity. The reason for this is that the current compressor is either on or off, which makes it rather inefficient. The new compressors are variable speed so can slow down or speed up depending on compressed air demand. With current air demand, the new compressors will use about £4,000 less electricity per month. As such, the new compressor units will pay for themselves in a little over 12 months.
There are additional benefits too, when you compress air, you generate heat. Normally, the compressors are air ventilated to disperse the heat. The compressors that we are purchasing will have a built-in heat exchanger that allows them to be water cooled. The compressors will be cooled by putting cold water in, and hot water will come out. The hot water that comes out of the compressors can then be fed to the site boiler. In effect the water to the boiler is being preheated so less gas is required in the boiler to heat the water.
New Boiler Burner
We have a steam boiler on site that produces steam to a distribution system around the site for various processes. The boiler is old but in very good condition. However, the gas burner unit that heats the water is very inefficient so the company has decided to replace the gas burner with a modern efficient unit.
The energy saving comes from the fact the current burner is either on to make steam and then off when enough steam has been made and until more steam is required. For safety reasons, when the boiler burner reignites to make more steam, it has to go through a purge cycle whereby the burner fan blows air through the burner combustion chamber to make sure there is no residual gas that may result in an explosion.
This purge cycle last for 90 seconds and whilst this process takes place, cold air is being blown through the boiler which cools it down. When the burner then restarts, the initial heating is to warm it back up after the cold purge cycle.
The new burner is a modulating burner which means the flame is on all the time and varies depending on steam demand so doesn’t need the purge cycle. This provides a considerable gas saving and as such will pay for itself in just over two years.
To view our ISO14001 accreditation, please click here, or to discover more about our environmental initiatives, please contact us.